Energy Efficient Upgrade of an Existing Building
Our Community project in Colchester is now nearing completion. In terms of the energy upgrade of an existing building it has explored many different approaches, all of which can be applied to existing solid masonry buildings of any size or type. The existing building has been both extended and upgraded. Below we list the series of technologies that have been applied.
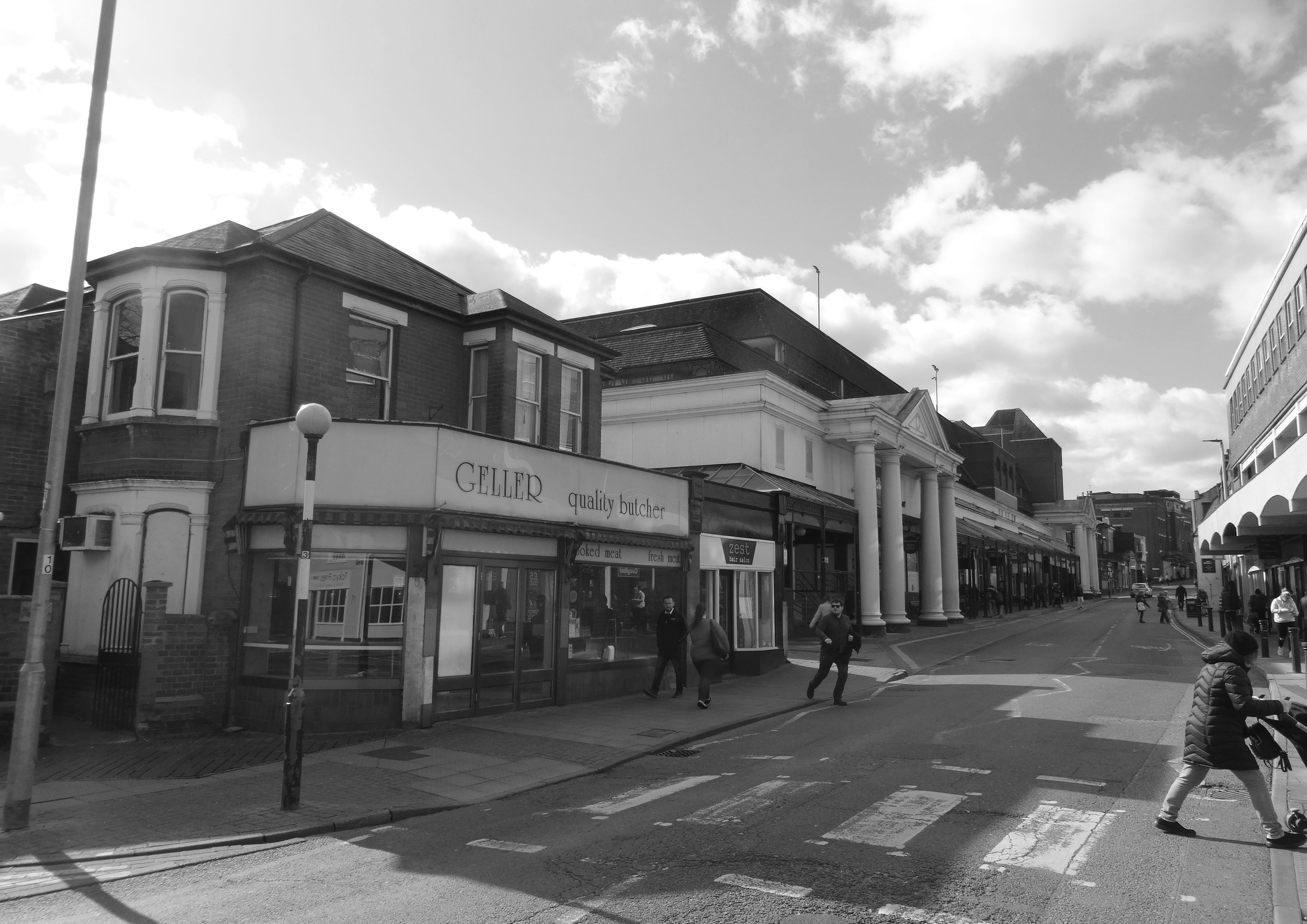
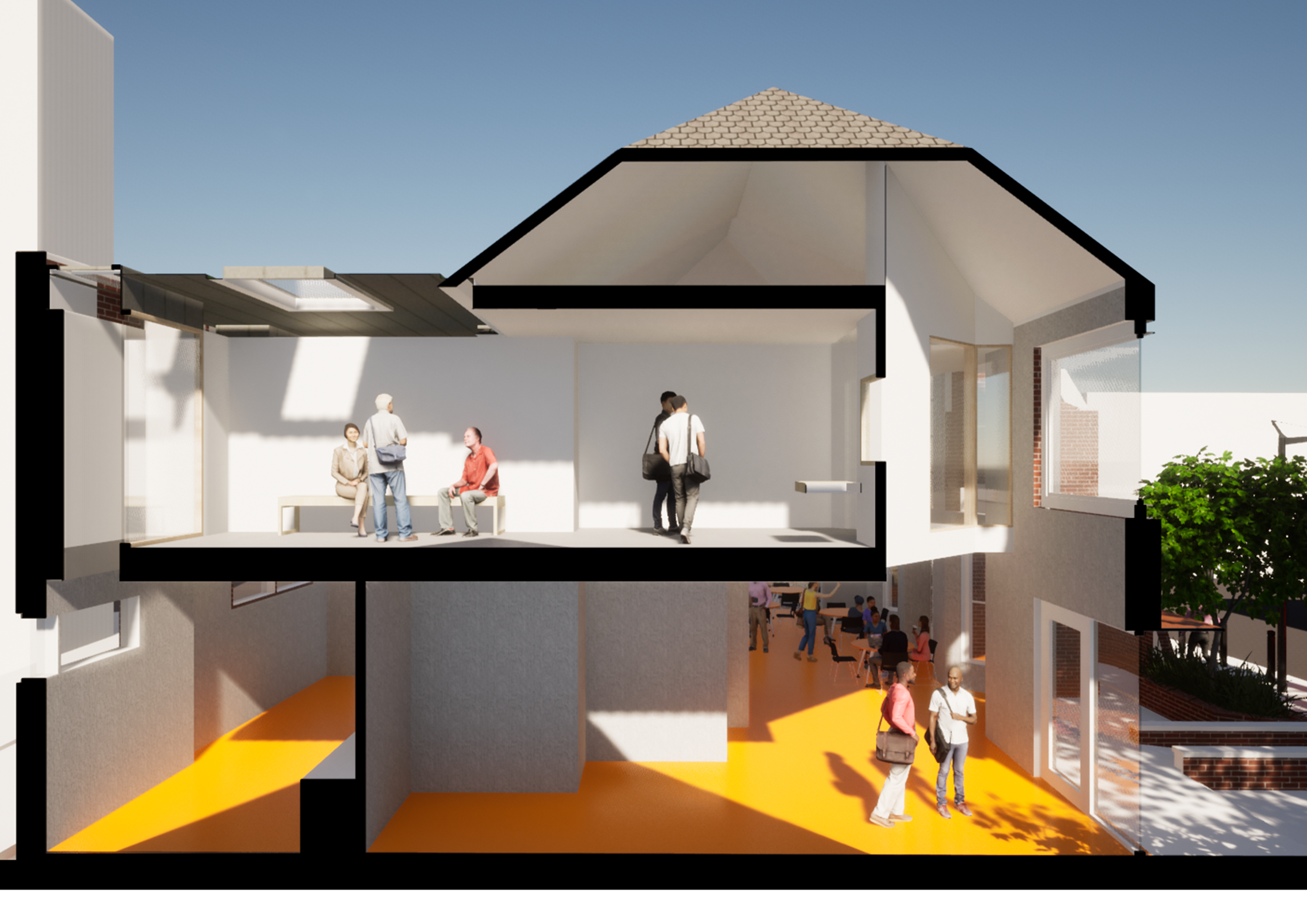
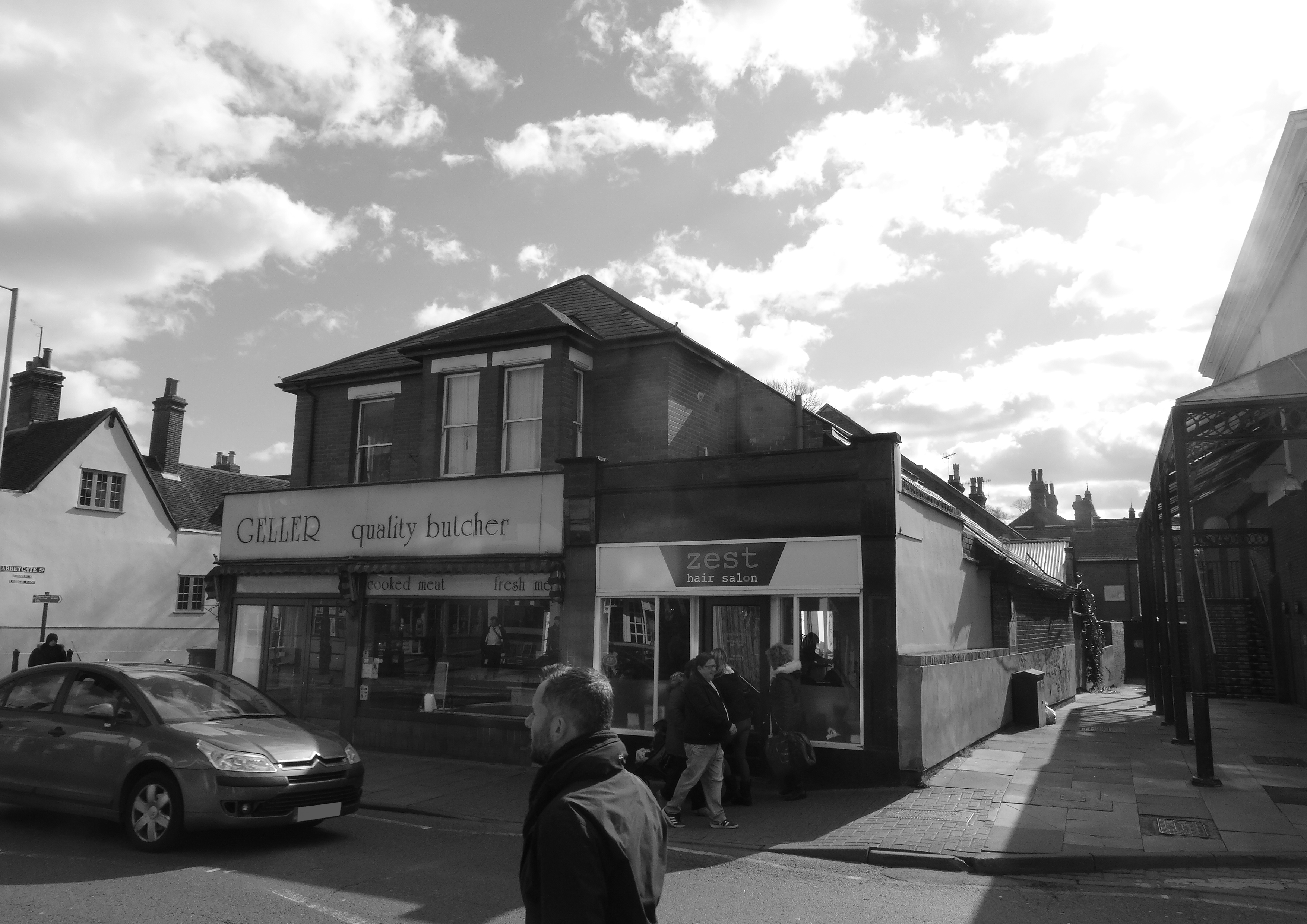
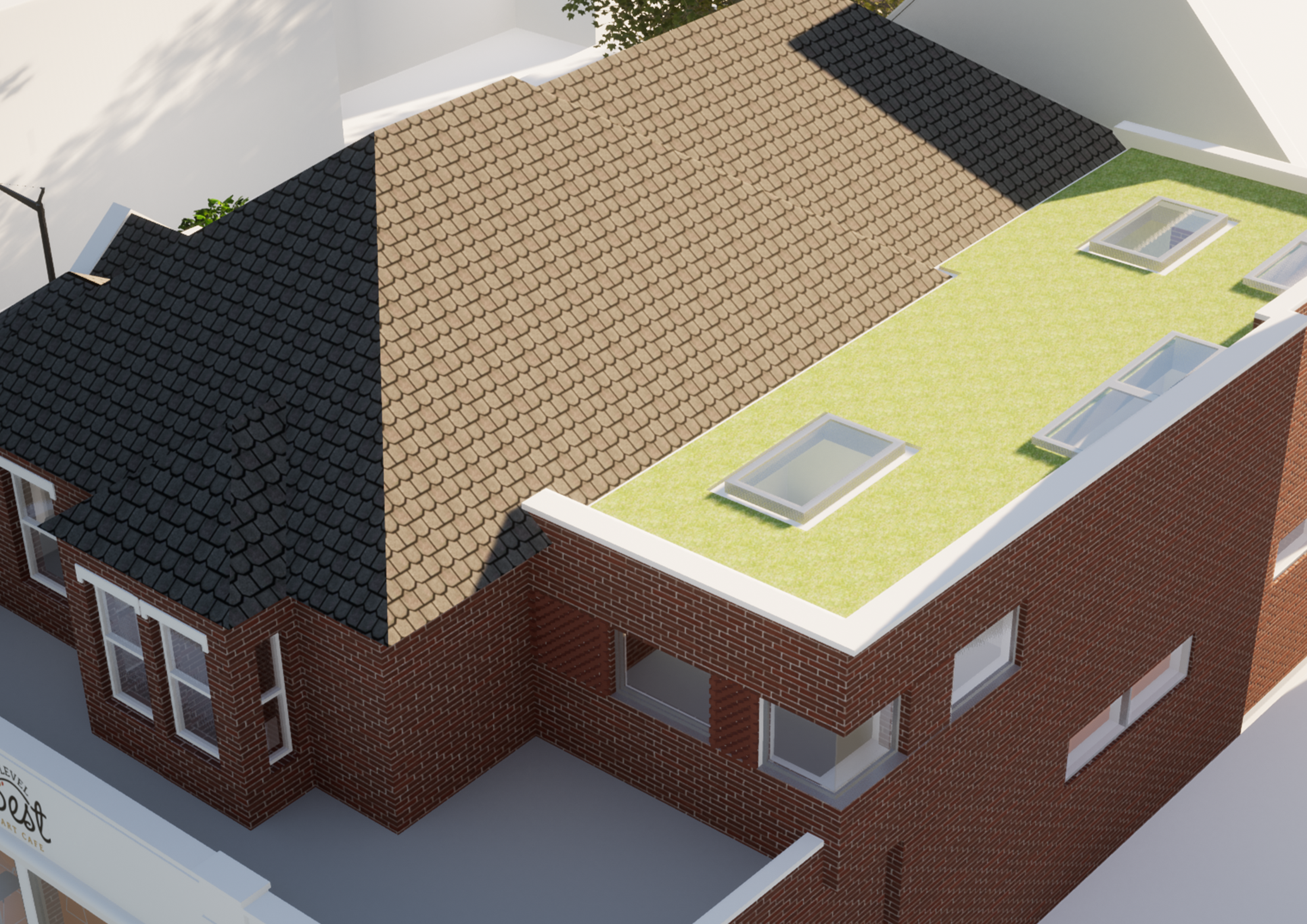
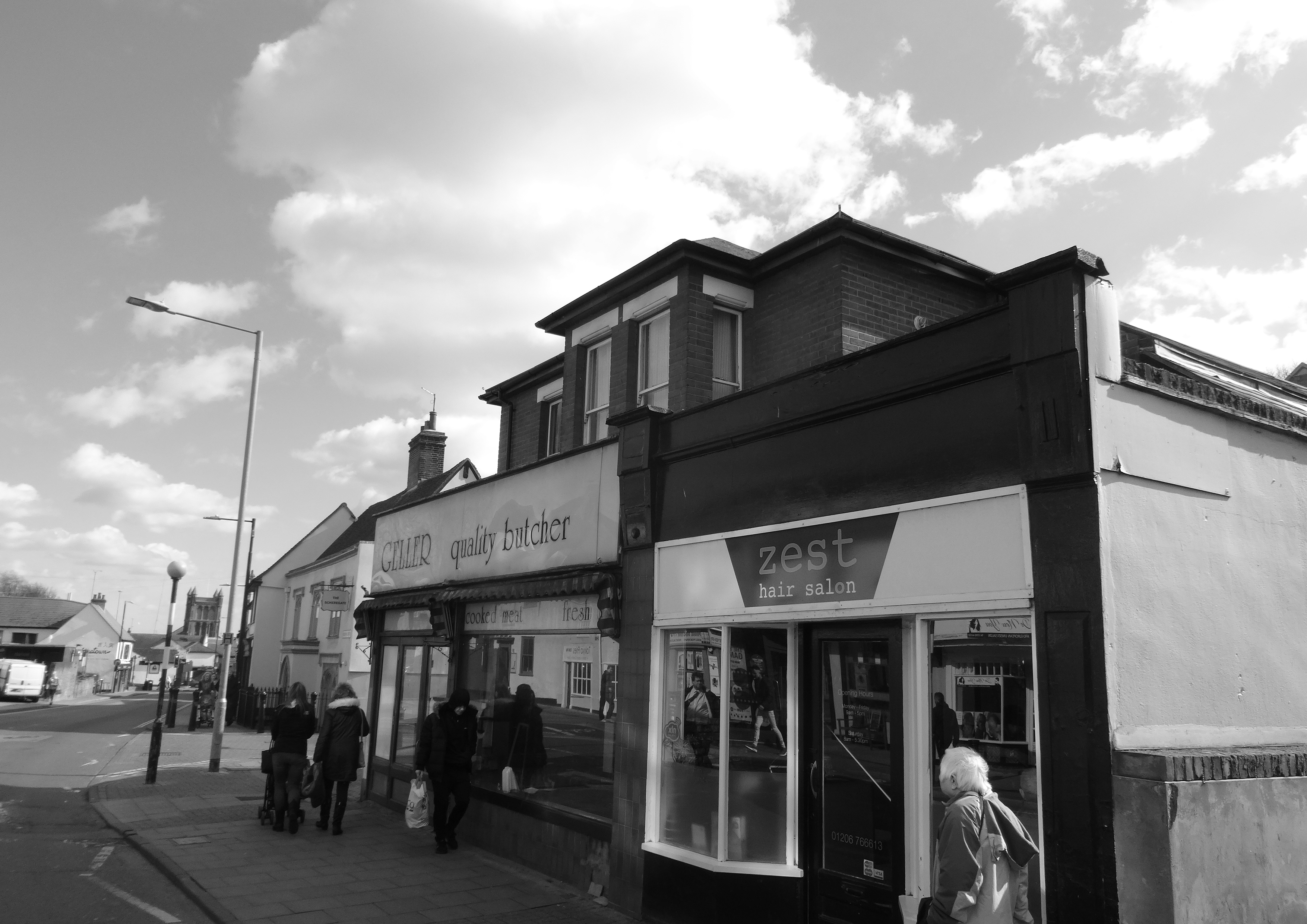
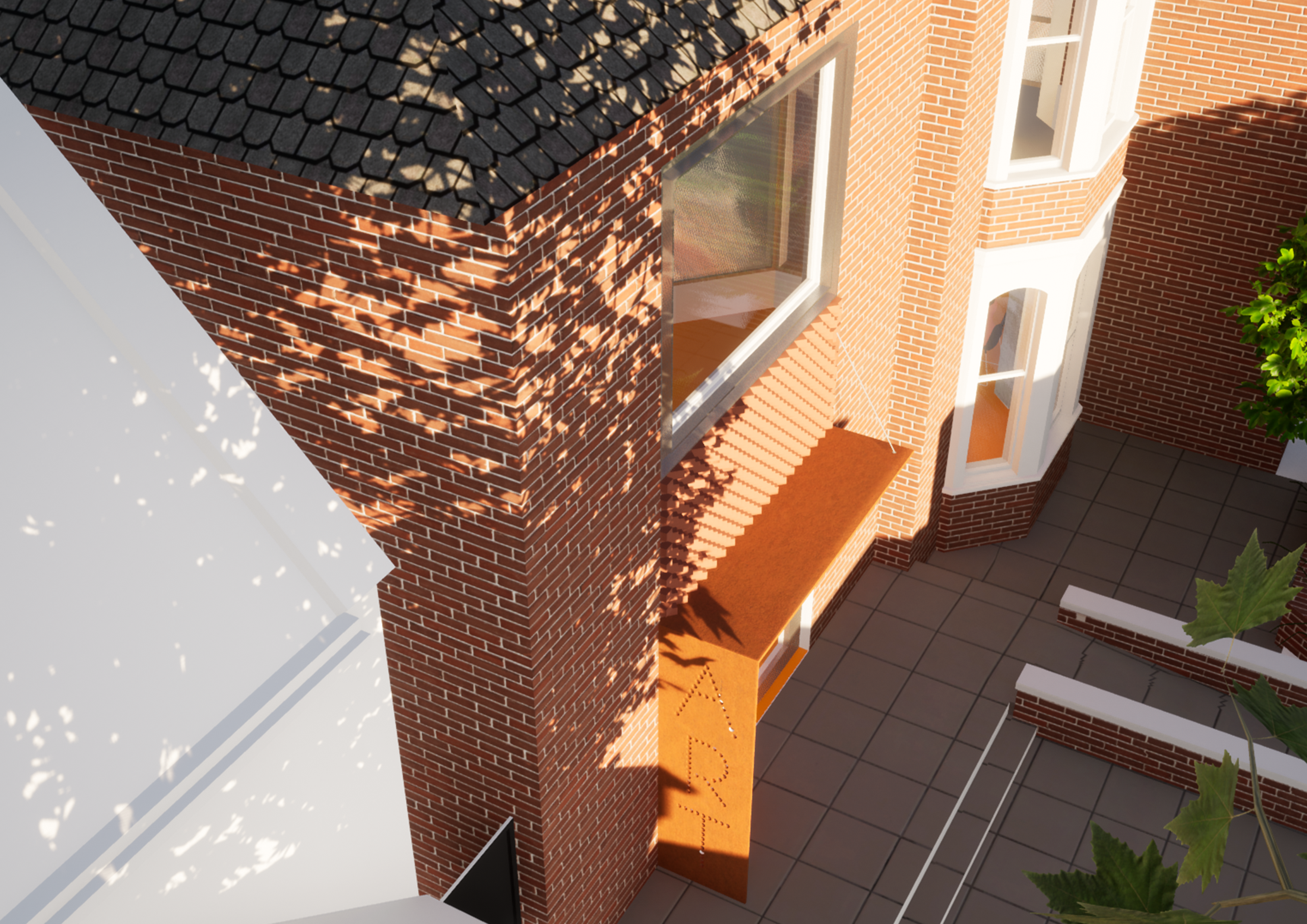
The thermal upgrade of existing solid brickwork walls
The existing solid brick walls are in many locations retained. Their energy performance is upgraded by lining the inside with a layer of insulation and plasterboard.
Here we thermally lined the inner face of the existing brick walls using the British Gypsum Gypliner System. This consists of two main components: the internal metal framing system and the suspended ceiling system.
The metal framing system is made of lightweight, corrosion-resistant metal, and is designed to support the plasterboard panels. The framing system can be fitted with insulation materials, such as mineral wool or glass wool, to reduce heat loss and improve the thermal performance of the room. In this case, mineral wool insulation was used due to its high thermal resistance, fire resistance, and sound insulation properties.
The insulation is typically placed between the plasterboard panels and the metal framing system, ensuring that it is sandwiched between two layers of materials. This enhances the thermal performance of the room, reducing heat loss and improving energy efficiency. Additionally, the insulation can also improve the acoustic performance of the room by reducing noise transmission and providing soundproofing.
The type and thickness of the insulation used will depend on the specific requirements of the project, such as the thermal performance and soundproofing requirements. For example, a thicker layer of insulation may be required in a room that requires high levels of thermal insulation, while a thinner layer may be sufficient in a room that requires less insulation.
Overall, the British Gypsum Gypliner System provides an effective solution for creating walls and ceilings that are energy-efficient, acoustically-friendly, and aesthetically-pleasing. By combining the metal framing system with mineral wool insulation, it helps to create a comfortable, low-carbon environment that supports sustainable living and reduces the carbon footprint of the building.
Replacement energy efficient windows
All existing timber framed windows were replaced with more energy efficient windows.
Thermally performing timber sash windows are designed to help reduce heat loss and improve energy efficiency in a building. The best options in the market typically incorporate a number of features to improve their thermal performance. These can include:
Double-glazing: The use of two panes of glass with a gap in between can help to reduce heat loss and increase insulation.
Low-E coatings: Low-emissivity coatings applied to the glass can reflect heat back into the room, helping to reduce heat loss.
Warm-edge spacers: Spacers between the panes of glass can also be made from materials that reduce heat loss, such as silicone or foam.
Draught-sealing: The sashes and frames should be designed to reduce air infiltration and improve the overall airtightness of the window.
High-quality materials: The sashes and frames should be made from materials with good insulation properties, such as timber, and should be well-manufactured to ensure a good fit.
There are many manufacturers that offer thermally performing timber sash windows. Some of the leading options include Timbawood, Wooden Windows Ltd, and Sash Windows London. The specific choice of window will depend on the individual requirements of the project, such as budget, architectural style, and performance requirements.
Airtight detailing around window openings
Airtight detailing around window openings refers to the measures taken to prevent air infiltration and reduce heat loss through the gap between the window and the surrounding wall. Proper airtight detailing is critical in ensuring the energy efficiency of a building. Some common techniques for airtight detailing around window openings include:
Window flashing: A flexible membrane is installed between the window and the surrounding wall to prevent air and water infiltration.
Tape or sealant: A silicone or rubber-based sealant is applied around the perimeter of the window frame to seal any gaps and prevent air infiltration.
Window gaskets: A rubber or foam gasket can be installed between the window frame and the wall to prevent air infiltration and improve insulation.
Interior window trim: A trim or casing can be installed around the interior of the window to conceal any gaps and improve the overall airtightness of the window.
Window wraps: A specially designed material, such as a window wrap, can be installed around the window to improve insulation and reduce air infiltration.
It’s important to note that proper airtight detailing around window openings requires careful design and execution. A combination of techniques may be used to achieve the best results, and the specific approach will depend on the type of window, the construction type, and the climate zone. Proper installation is also critical, and it’s important to use qualified professionals with experience in airtight detailing.
Low energy Light fittings
Low energy lighting refers to lighting systems that are designed to consume less energy compared to traditional lighting systems, while still providing adequate illumination. Withing this project all LED lights were installed in all cases. LED lights are highly efficient and consume less energy compared to traditional incandescent and fluorescent lighting. They are also longer-lasting and more durable.
MVHR System (Mechanical Ventilation Heat Recovery)
The project also incorporates an MVHR system. This stands for Mechanical Ventilation Heat Recovery.
The mechanical ventilation with heat recovery (MVHR) system in the community building plays a key role in ensuring the building is well-ventilated, energy-efficient, and comfortable for its occupants. The MVHR unit is designed to efficiently exchange air between the interior and exterior of the building, without wasting internal heating or cooling conditions.
The MVHR unit works by extracting air from the occupied areas of the building, filtering it to remove pollutants and particles, and then introducing it back into the interior. At the same time, the MVHR unit recovers heat from the outgoing air and transfers it to the incoming air. This process helps to reduce the amount of energy required for heating or cooling, making the building more energy-efficient and helping to lower energy costs.
Air Source Heat Pump
The space heating in the community centre is provided by an air source heat pump linked to underfloor heating.
The outdoor heat pump unit has a compressor, evaporating/condensing coil, and a fan. The fan coil units are connected to ceiling diffusers via supply side plenum boxes and rigid ductwork, allowing for precise temperature control. This system is common in buildings like this one.
The outdoor heat pump unit is a mini variable refrigerant flow heat pump, equipped with twin fans and R410A refrigerant. It is suitable for outdoor installation and has unique features, such as being a heat pump and heat recovery system for sizes 4, 5 and 6 HP.
Energy Management System
The building incorporates an energy management system. An energy management system (EMS) is a comprehensive system used to monitor and control the energy usage of a building. In the context of a community centre, an EMS would allow the building to be operated in the most energy-efficient manner possible, while ensuring comfort and safety for its occupants.
An EMS typically includes the following components:
Energy Monitoring: This involves using sensors and meters to measure the building’s energy usage in real-time. This data is then fed into the EMS software, where it can be analysed and used to identify areas for improvement.
Energy Control: The EMS software allows for the control of various energy-consuming systems in the building, such as lighting, HVAC, and appliances. This can include scheduling controls, occupancy sensors, and demand response systems.
Reporting: The EMS software generates detailed reports on the building’s energy usage, including energy consumption by system and by time of day. This information can be used to identify areas where energy usage can be reduced and track the impact of energy-saving measures over time.
Alarming: The EMS can also be programmed to send alarms and notifications to building staff in the event of equipment failure or energy usage that exceeds a certain threshold.
By implementing an energy management system in a community centre, building operators can gain a comprehensive understanding of the building’s energy usage and take actions to reduce energy consumption and costs. This, in turn, can help to reduce the building’s carbon footprint and promote sustainability.
Water Saving Measures
Water-saving measures play an important role in reducing the water consumption of larger community projects. Some common measures include:
Low-flow fixtures: Installing low-flow showerheads, toilets, and faucets can significantly reduce water usage without sacrificing performance.
Water recycling: Implementing systems to collect, treat, and reuse greywater (wastewater from showers, sinks, and washing machines) can reduce overall water consumption.
Rainwater harvesting: Collecting and storing rainwater for use in toilets, irrigation, and other non-potable applications can reduce the need for potable water.
Efficient irrigation: Installing efficient irrigation systems, such as drip irrigation or smart irrigation controllers, can help reduce water waste and ensure that water is being used where it is needed most.
In the context of this project low-flow fixtures were installed in all cases. With the sedum flat roof installation, water conservation measures are also an important consideration. Sedum roofs are designed to be partially or fully covered in vegetation, which helps reduce the amount of rainwater runoff and decrease the load on local water systems. By using drought-resistant plants and installing efficient irrigation systems, the water needs of the sedum roof can be further reduced, leading to additional water savings. Additionally, the sedum roof acts as an insulation layer, reducing the energy needs of the building and thus reducing the overall carbon footprint.
If you would like to discuss how your property could improve its energy efficiency in any way, please feel free to contact us at Shape Architecture